In the fast-paced world of industrial automation and precision engineering, the demand for reliable motor testing systems has never been higher. Whether you’re designing cutting-edge electric vehicles, optimizing renewable energy systems, or perfecting aerospace components, the backbone of your success lies in accurate data and robust equipment. Enter the realm of **hysteresis brakes**, **hysteresis dynamometers**, **hysteresis clutches**, and integrated **motor test systems**—technologies that redefine efficiency, control, and adaptability. Let’s dive into how these innovations are transforming industries worldwide.
---
### The Science Behind Hysteresis Technology 🔬
At the heart of hysteresis-based devices lies a simple yet powerful principle: the magnetic hysteresis effect. When a magnetic field is applied to certain materials, they resist changes in magnetization, creating a controllable braking or torque-generating force. This phenomenon eliminates mechanical contact, reducing wear and tear while delivering smooth, repeatable performance.
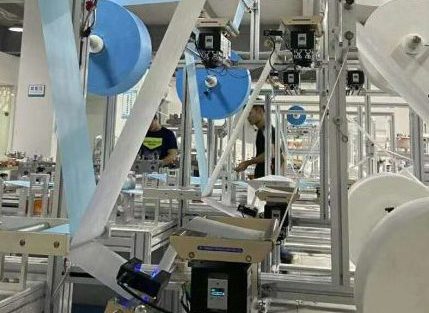
**Hysteresis Brakes**: Imagine a braking system with no friction pads, no heat degradation, and near-silent operation. These brakes use electromagnetic fields to generate resistance, making them ideal for applications requiring precise torque control—from conveyor systems to medical devices.
**Hysteresis Dynamometers**: Tired of inconsistent load simulations? These dynamometers provide non-contact torque measurement and dynamic load testing, essential for validating motors in electric vehicles or industrial machinery.
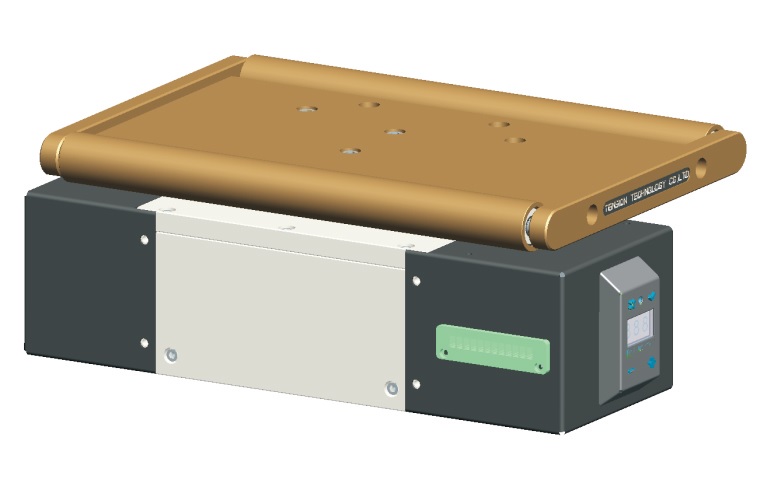
**Hysteresis Clutches**: Perfect for applications demanding slip-free power transmission, these clutches offer seamless engagement and disengagement, enhancing safety in robotics and assembly lines.
---
### Why Choose Hysteresis Over Traditional Systems? 🏆
Traditional mechanical systems often struggle with limitations like friction loss, maintenance costs, and limited scalability. Hysteresis-based solutions address these challenges head-on:
1. **Zero Contact, Zero Wear**
With no physical interaction between components, hysteresis devices dramatically extend operational lifespans. Say goodbye to Motor performance diagnostics of worn-out parts!
2. **Precision Control**
Adjust torque or load with micrometer-level accuracy using electronic controls. Ideal for R\u0026D labs where repeatability is non-negotiable.
3. **Silent Operation**
Eliminate the clatter of gears or belts. Hysteresis systems operate quietly, making them suitable for noise-sensitive environments like hospitals or offices.
4. **Scalability**
From micro-motors in drones to megawatt turbines, hysteresis technology adapts effortlessly to varying power ranges.
---
### Motor Test Systems: The Unsung Heroes of Innovation 🔧
Behind every high-performance motor is a rigorous testing phase. Modern **motor test equipment** goes beyond basic functionality checks—it simulates real-world conditions, predicts failures, and optimizes efficiency.
**Key Features of Advanced Motor Test Systems**:
- **Dynamic Load Simulation**: Test motors under fluctuating loads to mimic actual operating conditions.
- **Energy Recovery**: Regenerative systems recycle up to 90% of energy used during testing, slashing electricity costs.
- **Data Analytics Integration**: AI-powered software analyzes terabytes of data to identify trends, inefficiencies, or potential defects.
Aerospace giants, for instance, rely on these systems to ensure helicopter rotors withstand extreme temperatures. Meanwhile, EV manufacturers use them to validate battery-motor synergy for maximum range.
---
### Case Study: Hysteresis in Action 🚗
Let’s look at a real-world example. A leading electric vehicle manufacturer faced challenges in testing their next-gen powertrain. Traditional dynamometers caused vibration issues and inaccurate readings. By switching to a **hysteresis dynamometer**, they achieved:
- 40% faster test cycles due to instant load adjustments.
- 15% improvement in energy efficiency during regenerative braking simulations.
- Zero maintenance downtime over 12 months of continuous operation.
---
### The Future of Motor Testing: Trends to Watch 🌐
As industries push toward sustainability and automation, motor test systems are evolving rapidly:
1. **IoT-Enabled Smart Testing**
Remote monitoring and predictive maintenance via cloud-connected devices reduce on-site labor and prevent unexpected breakdowns.
2. **Green Testing Solutions**
Energy-recovering dynamometers align with corporate carbon neutrality goals, turning test labs into eco-friendly hubs.
3. **Customizable Modular Systems**
Plug-and-play configurations allow engineers to mix components (e.g., hysteresis brakes + torque sensors) for tailored solutions.
---
### Choosing the Right Partner for Your Needs 🤝
Not all hysteresis products are created equal. When selecting a supplier, prioritize:
- **Certifications**: ISO compliance and industry-specific approvals (e.g., automotive, aerospace).
- **Technical Support**: 24/7 access to engineers for troubleshooting or system upgrades.
- **Scalability**: Can the equipment grow with your business?
Brands like [Your Company Name] stand out by offering end-to-end solutions—from consulting to post-installation audits—ensuring your motor testing infrastructure is future-proof.
---
### Final Thoughts: Elevate Your Testing Game 🚀
In a world where milliseconds and microns matter, settling for outdated testing methods isn’t an option. Hysteresis technology bridges the gap between precision and practicality, empowering industries to innovate faster, safer, and smarter. Whether you’re refining a miniature servo motor or a hydroelectric turbine, the right test system isn’t just an investment—it’s your competitive edge.
Ready to revolutionize your motor testing process? Explore hysteresis-based solutions today and join the ranks of pioneers shaping tomorrow’s technologies. 💡
---
[Your Company Name] – Where Precision Meets Performance. 🔋⚡